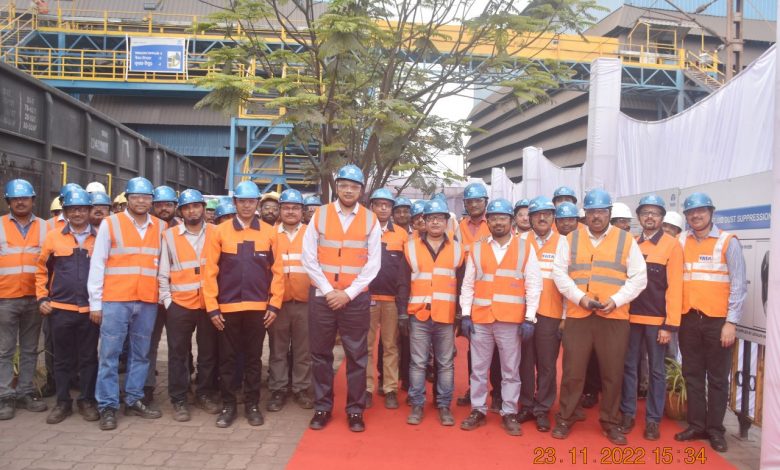
Bhubaneswar: Tata Steel Meramandali, located in Dhenkanal district of Odisha, has introduced model wagon tippler with the use of state-of-the-art robots at its Raw Material Handling Systems (RMHS) operations to eliminate man-machine interface during the unloading of wagons.
Peeyush Gupta, Vice President, Supply Chain and Group Strategic Procurement (Designate), Tata Steel and Subodh Pandey, Vice President, Operations, Tata Steel Meramandali formally inaugurated the man-less model wagon tippler here on November 23, 2022. With this new system, the entire unloading and tippling operations have now been automated. This has eliminated the human-machine interface hence ensuring safety and contributing to enhanced productivity.
Peeyush Gupta, Vice President, Supply Chain and Group Strategic Procurement (Designate), Tata Steel, said: “This achievement is a stellar example of how working in teams can solve a problem with seemingly no solution. This fool proof safety initiative is a classic example of Poka-Yoke. The innovations which have been implemented are first of its kind even for our Jamshedpur and Kalinganagar plants. RMHS is an area which has many risks, and the team is continuously working to eliminate the identified risks through various safety initiatives. This Model Wagon Tippler will significantly reduce the rake unloading cycle time in a safe manner.”
Subodh Pandey, Vice President, Operations, Tata Steel Meramandali, said: “We are continuously adopting the best available technologies to upgrade facilities in our integrated steel operations to improve safety, environment, productivity and reliability. This is an excellent illustration of integration of advanced technologies to solve all issues of wagon tippler operation. The new system, installed at Wagon Tippler II, will be horizontally deployed in others as well.”
The rake tippling operations at RMHS of the steel plant involve critical activities that includes decoupling, rotation, alignment and coupling of the wagons at both the inhaul and outhaul side. This is followed by wagon cleaning in the end. The newly installed systems include automatic drop gates with laser curtains, robotic decoupling and coupling operation, smart access control inside tippler complex, wagon cleaning system and automatic side arm charger operation resulting in significant reduction of high risk activities. This system is also supplemented by a uniquely designed smart fencing system with automated gate locking facility for restricting unauthorised entry during equipment operation.